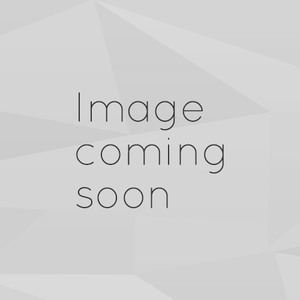
8.3 Pillow Film is a premium air cushion packaging solution designed to provide superior protection for goods during storage and transportation. Engineered for efficiency and durability, this film is used to create air pillows that act as a lightweight yet highly effective void fill material.
The ClimaFilm50 AirWave 8.3 Pillow Film in 4 Chamber Quilt format is designed for use in protective packaging operations that demand both reliability and efficiency. Measuring 420mm in width and supplied in a 450-metre roll, this film creates four connected air cushions per row, forming a quilted layer that distributes pressure evenly across packed items.
Four-Chamber Cushioning Structure
Each row features four uniform chambers that inflate to create a continuous quilt of air-filled pillows. This layout is especially effective at reducing impact during transit, offering both surface protection and void filling. The even pressure distribution helps reduce product movement within the outer packaging, particularly useful for items with flat or fragile surfaces.
Designed for AirWave Machines
Manufactured to work with AirWave 8.3 systems, this ClimaFilm50 variant enables efficient integration into modern packing stations. Its controlled inflation and precise sealing create uniform chambers that retain air reliably, reducing the risk of deflation during shipment. The film’s clarity and strength also contribute to product visibility and protection.
Applications and Benefits
This quilted air pillow film is suitable for securing electronics, boxed items, cosmetics, and printed materials. The 420mm width covers more surface area per pass compared to standard pillow formats, making it ideal for packing larger cartons or providing full-surface coverage at the base or top of boxes.
Product Specifications:
- 4 chamber quilt structure for stability
- 420mm wide, 450m long roll
- High-strength ClimaFilm50 material
- Compatible with AirWave 8.3 systems
- Lightweight cushioning for various goods
The quilt format offers a practical alternative to traditional void fill, combining speed, precision, and flexibility across multiple packaging environments.